Are you struggling to choose between 304 vs 316 Stainless Steel for your project? Wondering which alloy offers better corrosion resistance, strength, or cost-effectiveness? Are you unsure how their unique properties will impact the success of your specific application?
The main difference between 304 vs 316 Stainless Steel lies in their corrosion resistance and composition. 304 stainless steel is a cost-effective and versatile option suitable for most indoor and outdoor environments, providing strong resistance to rust and oxidation. However, 316 stainless steel, with its added molybdenum content, offers superior protection against harsh chemicals and saltwater, making it the better choice for marine, pharmaceutical, and industrial settings. If your project requires exposure to chlorides, extreme environments, or corrosive chemicals, 316 stainless steel is the recommended option. Otherwise, 304 stainless steel remains an excellent, budget-friendly choice.
Both alloys are exceptional, but their differences make them suited for distinct applications. By exploring their chemical compositions, corrosion resistance, price points, and applications, you can confidently select the most suitable material for your project. Read on to discover the nuances of 304 vs 316 Stainless Steel and make an informed choice for long-term success.
Overview of Stainless Steel Grades
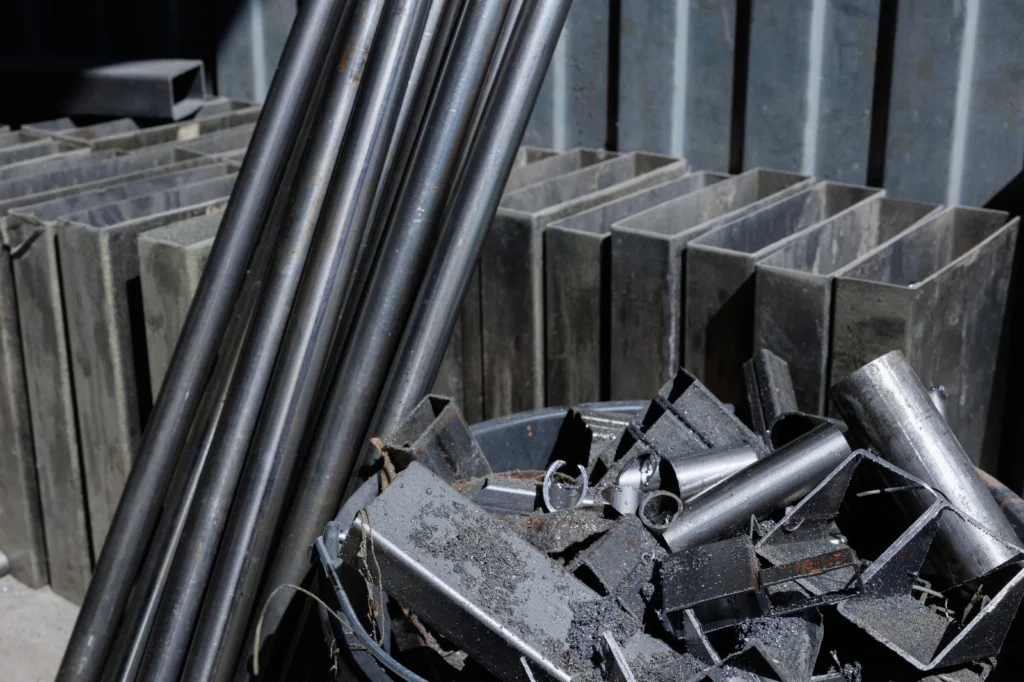
Stainless steel is a versatile alloy widely used across industries for its strength, corrosion resistance, and durability. It is categorized into different grades based on its chemical composition and mechanical properties. The three primary categories of stainless steel are:
- Austenitic Stainless Steel: These grades, such as 304 vs 316 stainless steel , are the most commonly used. They are highly resistant to corrosion, non-magnetic, and easily weldable, making them suitable for a wide range of applications.
- Ferritic Stainless Steel: Magnetic and less corrosion-resistant than austenitic grades, ferritic stainless steel is often used in automotive and industrial applications.
- Martensitic Stainless Steel: Known for high hardness and strength, this type is used in applications like knives and cutting tools but has limited corrosion resistance compared to other grades.
Each category offers unique advantages, but austenitic grades like 304 vs 316 stainless steel are the most popular due to their excellent corrosion resistance and versatility.
Need Help? We’re Here for You!
Why Choosing the Right Stainless Steel Grade Matters?
Choosing the right grade of stainless steel is crucial for ensuring your project’s success. Each grade is designed to meet specific environmental and performance needs. Selecting an unsuitable grade can lead to premature corrosion, structural failures, or increased maintenance costs.
For example, a general-purpose grade like 304 stainless steel is an economical option for everyday applications, but it may not perform well in chloride-rich environments, where 316 stainless steel excels. Understanding the strengths and limitations of each grade enables you to choose a material that balances performance and cost effectively.
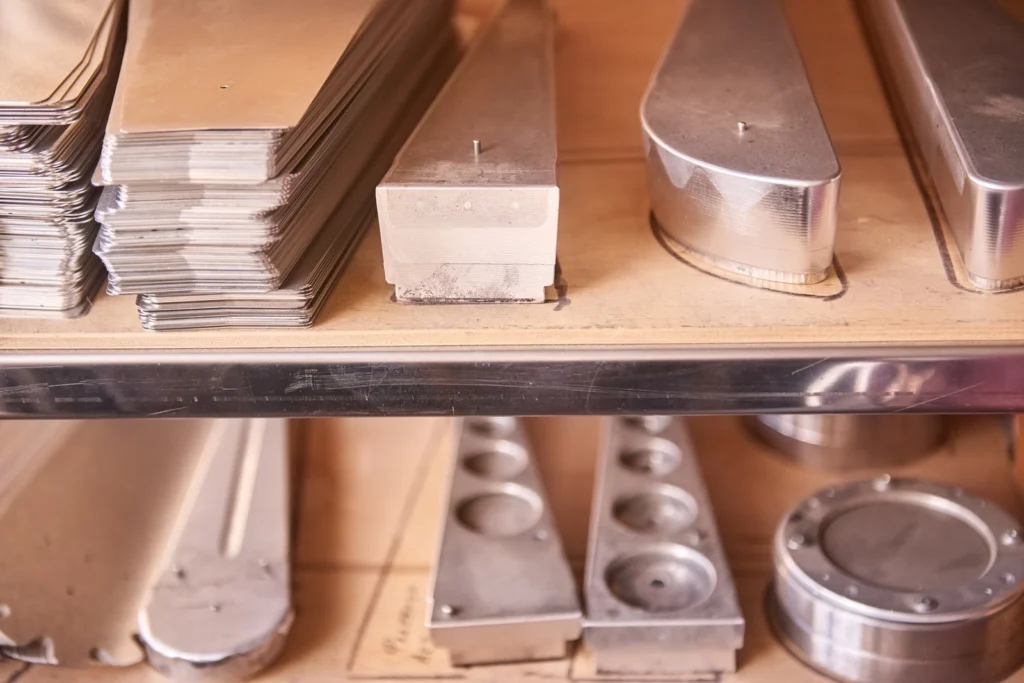
In this article, we’ll compare 304 vs 316 Stainless Steel, the two most widely used grades in the austenitic category. While they share similar characteristics, their differences in composition and performance make them suitable for distinct applications. Whether you’re working on a kitchen appliance, a marine structure, or an industrial setup, understanding these two grades will help you make the best choice for your project.
304 Stainless Steel: Composition and Properties
Chemical Composition of 304 Stainless Steel
304 stainless steel is one of the most widely used austenitic stainless steels, offering an excellent balance of corrosion resistance, strength, and affordability. Its composition includes approximately 18-20% chromium and 8-10.5% nickel, both of which contribute to its durability and resistance to oxidation.
The chromium content forms a protective oxide layer on the surface, shielding the material from rust in normal atmospheric conditions. Nickel, on the other hand, enhances the alloy’s toughness and resistance to stress corrosion cracking. Other trace elements include:
- Carbon (≤ 0.08%): Improves tensile strength while maintaining weldability.
- Manganese (≤ 2%): Increases strength and wear resistance.
- Silicon (≤ 0.75%): Enhances oxidation resistance.
- Phosphorus and Sulfur: Present in minimal amounts to improve machinability.
One notable difference in the comparison of 304 vs 316 stainless steel is the absence of molybdenum in 304 stainless steel, which limits its corrosion resistance in chloride-heavy environments, such as coastal areas or marine applications. While 304 stainless steel resists rust in most standard environments, prolonged exposure to chlorides can lead to localized corrosion like pitting or crevice corrosion.
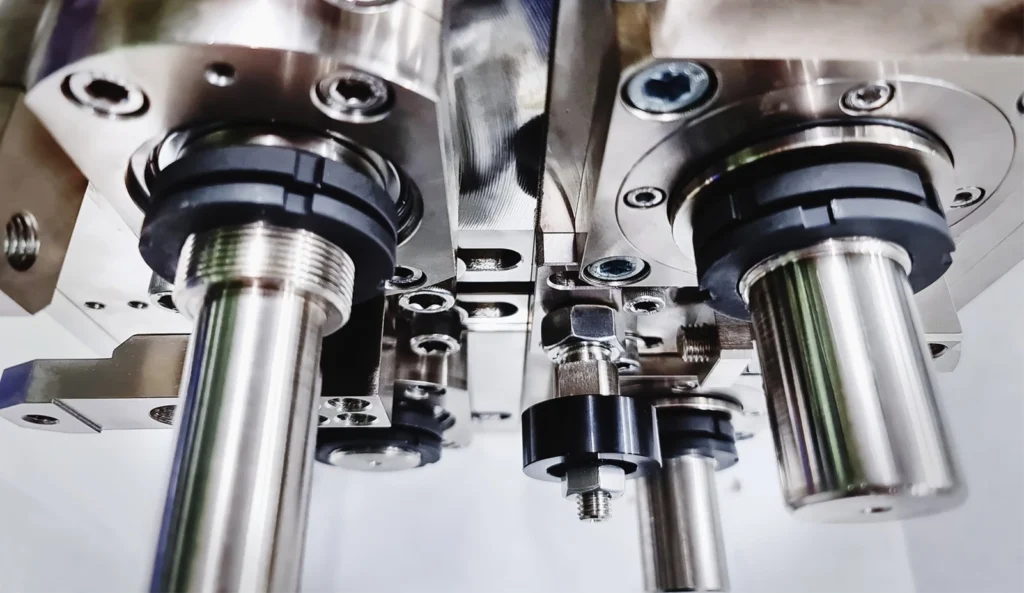
Key Properties of 304 Stainless Steel
304 stainless steel is highly valued for its versatility and excellent performance in a wide range of applications. Its key properties include:
- Corrosion Resistance
The alloy performs exceptionally well in standard atmospheric conditions, resisting rust and oxidation in everyday environments. However, it is less suited for highly corrosive settings, such as those involving saltwater or acidic chemicals, where 316 stainless steel outperforms it. This limitation highlights a key aspect of 304 vs 316 stainless steel, making 304 stainless steel ideal for indoor or general-purpose applications where exposure to aggressive agents is minimal. - Strength and Durability
Known for its high tensile strength and durability, 304 stainless steel maintains its integrity under moderate mechanical stress and a broad range of temperatures. These attributes make it reliable for structural and industrial uses. However, when comparing 304 vs 316 stainless steel, 316 stainless steel provides a better solution in harsh environments where extreme corrosion resistance or additional durability is required. - Magnetic Behavior
While 304 stainless steel is generally non-magnetic, it can become slightly magnetic when subjected to processes like cold-working or forming. This minor magnetic property is typically not an issue for most applications but is worth considering for projects requiring non-magnetic materials. - Cost Efficiency
One of the key advantages of 304 stainless steel is its affordability. Its simpler composition and widespread availability make it a cost-effective option for a wide range of industries. For projects that prioritize budget and do not involve exposure to harsh environments, 304 stainless steel is a practical choice.
Finally, 304 stainless steel is also a common material in food-related applications due to its non-reactive surface. Its composition prevents contamination and ensures that no harmful substances leach into food, making it a safe and reliable option for food storage, processing, and preparation equipment.

Get Your Free Catalog Now!
316 Stainless Steel: Composition and Properties
Chemical Composition of 316 Stainless Steel
316 stainless steel is a high-performance austenitic stainless steel designed for environments that demand exceptional corrosion resistance. In the comparison of 304 vs 316 stainless steel, both share similarities in chromium and nickel content, but 316 stainless steel includes 2-3% molybdenum, which significantly enhances its ability to resist chloride-induced corrosion.
The composition of 316 stainless steel includes:
- 16-18% Chromium: Provides corrosion resistance by forming a protective oxide layer.
- 10-14% Nickel: Enhances toughness and resistance to stress corrosion cracking.
- 2-3% Molybdenum: Offers superior protection against pitting and crevice corrosion caused by chlorides.
- Trace Elements:
- Carbon (≤ 0.08%): Improves hardness and strength while retaining good weldability.
- Manganese (≤ 2%) and Silicon (≤ 0.75%): Improve oxidation resistance and material stability.
- Phosphorus and Sulfur: Present in minimal quantities to enhance machinability.
This enhanced composition makes 316 stainless steel particularly effective in environments where 304 vs 316 stainless steel performance differs, such as in marine and chemical processing applications. However, despite its superior corrosion resistance, it is not entirely immune to rusting. Under extreme conditions, such as prolonged exposure to concentrated acids or high levels of chlorides, localized corrosion like pitting may still occur.
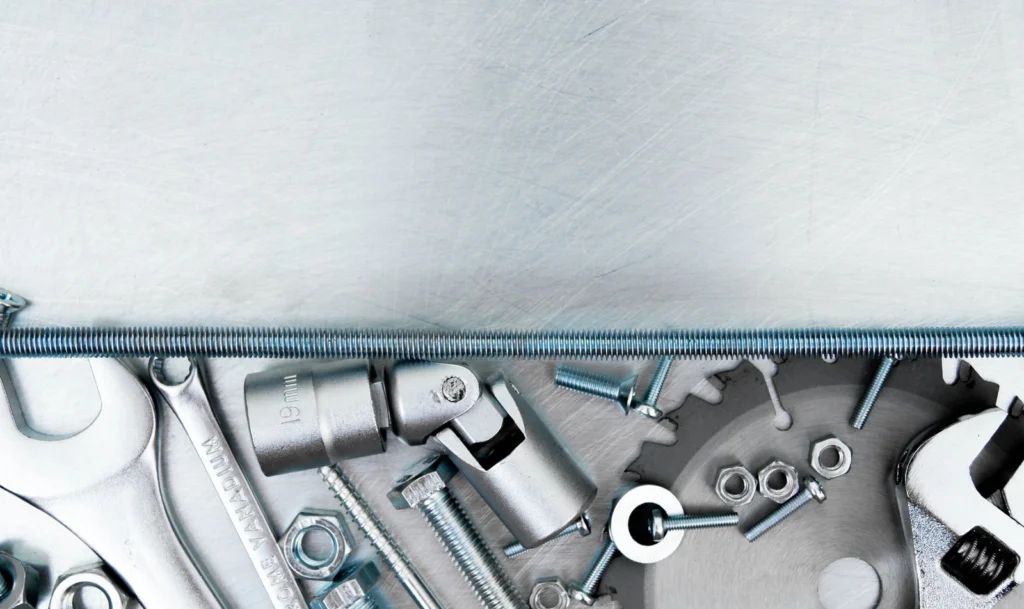
Key Properties of 316 Stainless Steel
The properties of 316 stainless steel are a direct result of its unique composition, making it a material of choice for harsh environments.
- Corrosion Resistance
The addition of molybdenum significantly improves 316 stainless steel’s ability to resist corrosion, particularly in chloride-heavy environments like saltwater or areas exposed to deicing salts. In the comparison of 304 vs 316 stainless steel, 316 stainless steel outperforms 304 stainless steel in its resistance to pitting, crevice corrosion, and overall degradation in chemically aggressive conditions. This superior corrosion resistance is why 316 stainless steel is often used in marine, pharmaceutical, and industrial settings. - Strength and Heat Resistance
Like 304 vs 316 stainless steel boasts excellent tensile strength and durability. Additionally, its resistance to high temperatures makes it suitable for applications like heat exchangers and industrial ovens, where elevated temperatures are common. It retains its structural integrity and resists scaling better than 304 stainless steel under prolonged heat exposure. - Non-Magnetic Properties
Similar to 304 vs 316 stainless steel is non-magnetic in its annealed state. However, slight magnetism may develop during cold-working processes, such as bending or forming. - Cost Implications
The inclusion of molybdenum and its superior corrosion resistance make 316 stainless steel more expensive than 304 stainless steel. However, when evaluating 304 vs 316 stainless steel, this higher cost is often justified for projects requiring long-term durability in extreme environments, as it reduces maintenance needs and extends the material’s lifespan. By incorporating molybdenum into its composition, 316 stainless steel offers superior corrosion resistance, particularly in chloride-rich environments like saltwater and chemical exposure. Its enhanced durability and heat resistance make it ideal for demanding applications in marine, pharmaceutical, and industrial settings. Although more expensive than 304 stainless steel, its performance in harsh conditions justifies the cost, making it the preferred choice for projects requiring long-term reliability and minimal maintenance.
Applications of 304 vs 316 Stainless Steel
The versatility of 304 vs 316 stainless steel has made them essential materials in numerous industries. While both grades are durable and corrosion-resistant, their unique properties determine their suitability for specific applications. Understanding these applications helps ensure the right material is selected for optimal performance and cost-efficiency.
Where 304 Stainless Steel Is Best Used?
304 stainless steel is highly valued for its affordability and versatility, making it the most commonly used stainless steel in general-purpose applications. Its key uses include:
Kitchen Equipment and Appliances
304 stainless steel is widely used in sinks, cookware, cutlery, and countertops. Its non-reactive surface prevents contamination and makes it safe for food preparation.
It resists oxidation and cleaning chemicals, ensuring longevity in kitchen environments.
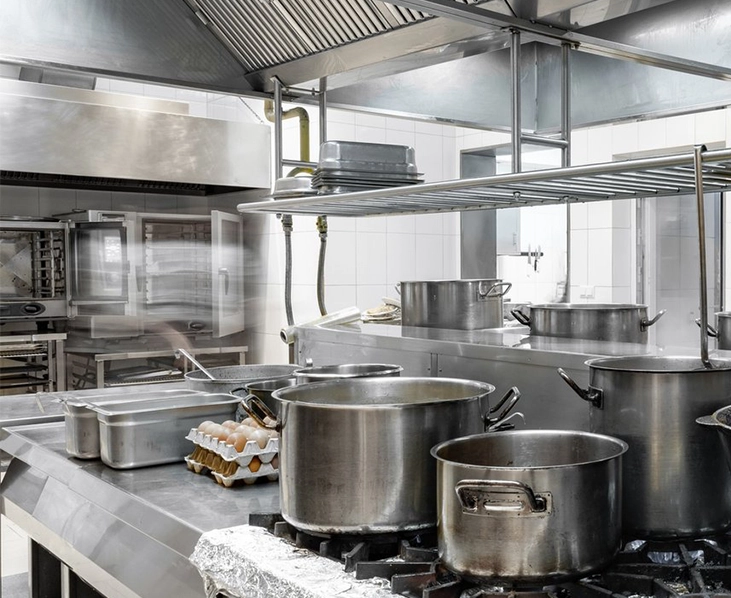
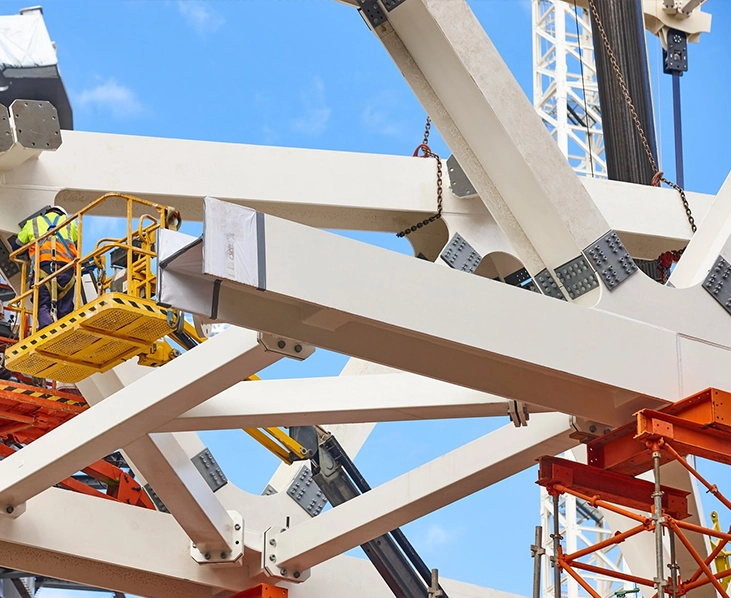
Construction and Architecture
Frequently used for handrails, cladding, and structural components, 304 stainless steel is favored for its strength and aesthetic appeal.
Its corrosion resistance makes it suitable for indoor and outdoor applications, provided the exposure to chlorides or harsh conditions is minimal.
Automotive and Transportation
Found in exhaust systems, trims, and decorative parts, 304 stainless steel combines durability with cost-effectiveness.
It performs well under moderate mechanical stress and typical atmospheric conditions.
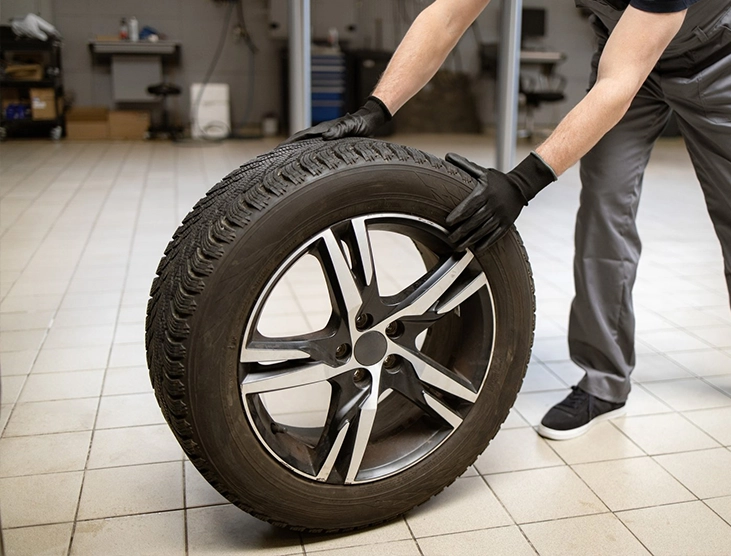
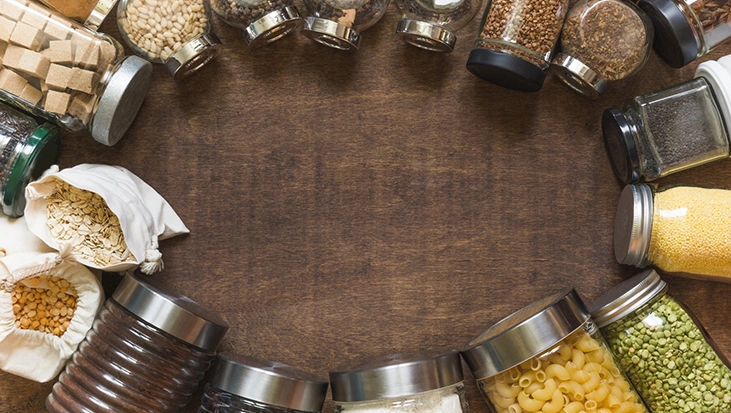
Medical and Food Storage
Due to its food-safe properties and resistance to bacteria accumulation, 304 stainless steel is used in food storage containers and surgical instruments for non-corrosive environments.
Where 316 Stainless Steel Excels
316 stainless steel, with its molybdenum-enhanced composition, is designed for demanding applications where resistance to harsh conditions is critical. Key uses include:
- Marine Environments
- 316 stainless steel is the go-to material for boat fittings, docks, and offshore platforms. Its resistance to saltwater corrosion makes it indispensable for coastal and underwater applications.
- Chemical Processing
- Frequently used in chemical storage tanks, reactors, and pipelines, 316 stainless steel withstands exposure to strong acids, alkalis, and chlorides.
- It is commonly used in the pharmaceutical industry, where contamination and corrosion resistance are critical.
- Medical and Surgical Applications
- Its biocompatibility and superior corrosion resistance make 316 stainless steel ideal for surgical implants, tools, and sterilization equipment.
- Industrial Equipment
- Heat exchangers, industrial ovens, and heavy-duty machinery components benefit from 316 stainless steel’s ability to endure high temperatures and harsh chemicals.
Key Differences Between 304 vs 316 Stainless Steel
The differences between 304 vs 316 stainless steel stem from their composition, performance, and cost. These distinctions determine their suitability for specific environments and applications. Below is a side-by-side comparison to help you make an informed choice.

Get Your Free Catalog Now!
304 vs 316 Stainless Steel
Feature | 304 Stainless Steel | 316 Stainless Steel | Key Difference |
---|---|---|---|
Chemical Composition | 18-20% Chromium, 8-10.5% Nickel, no Molybdenum | 16-18% Chromium, 10-14% Nickel, 2-3% Molybdenum | The addition of molybdenum in 316 provides enhanced corrosion resistance in harsh environments. |
Corrosion Resistance | Good for general environments | Superior, especially in saltwater or chemical exposure | 316 stainless steel resists pitting and crevice corrosion, making it ideal for marine and industrial applications. |
Strength and Durability | High tensile strength for general-purpose use | Higher tensile strength and durability in extreme conditions | 316 stainless steel offers greater reliability under stress and in corrosive environments. |
Heat Resistance | Can handle temperatures up to 870°C (1600°F) | Performs well up to 925°C (1700°F) | Both grades offer excellent heat resistance, but 316 has a slight edge in high-temperature applications. |
Cost | Lower due to simpler composition | Higher due to molybdenum content | 304 stainless steel is cost-effective for everyday use, while 316 justifies its higher price in challenging conditions. |
Magnetic Properties | Non-magnetic in annealed state, slightly magnetic when cold-worked | Non-magnetic in annealed state, may also exhibit slight magnetism when cold-worked | Both are generally non-magnetic but can become slightly magnetic after cold-working. |
Applications | Kitchen equipment, construction, automotive parts | Marine environments, chemical processing, medical devices | 304 stainless steel suits general applications, while 316 excels in demanding and corrosive environments. |
Factors to Consider When Choosing 304 vs 316 Stainless Steel
Choosing between 304 vs 316 stainless steel depends on multiple factors, including environmental conditions, budget, longevity requirements, and the specific demands of your project. While both grades are durable and corrosion-resistant, understanding these considerations can help you select the most suitable option.
Environmental Conditions
The environment in which the material will be used is a crucial factor. 304 stainless steel works well in standard environments where exposure to corrosive elements is minimal. However, in harsh conditions such as coastal areas, marine settings, or industrial environments with high chloride or chemical exposure, 316 stainless steel provides superior performance. When deciding between 304 vs 316 stainless steel, consider whether the material will face frequent contact with saltwater, moisture, or aggressive chemicals.
Need Help? We’re Here for You!
Budget and Cost Considerations
Cost is a significant factor when comparing 304 vs 316 stainless steel. 304 stainless steel is more affordable due to its simpler composition, making it an excellent choice for budget-conscious projects. On the other hand, while 316 stainless steel has a higher upfront cost, its durability and resistance to corrosion in challenging environments often lead to reduced maintenance and replacement costs over time. Evaluate the long-term value of your investment when making your decision.
Longevity and Durability Needs
The lifespan of the material is another key consideration. If your project demands a material with excellent durability in corrosive environments, 316 stainless steel is the better choice. Its molybdenum content enhances resistance to pitting and crevice corrosion, ensuring a longer service life in aggressive conditions. For less demanding applications, 304 stainless steel provides a reliable and cost-effective option without compromising quality.
Matching Material to Specific Applications
When comparing 304 vs 316 stainless steel, it’s essential to match the material to your project’s specific requirements:
- Food Applications: Both grades are safe for food use, but 316 stainless steel is preferred in environments with high salt exposure or frequent cleaning with harsh agents.
- Medical and Pharmaceutical Use: The biocompatibility of 316 stainless steel makes it ideal for surgical tools, implants, and chemical containment systems.
- Decorative and Structural Applications: If aesthetic appeal and cost-efficiency are priorities, 304 stainless steel is an excellent choice for handrails, cladding, and interior fixtures.
Aesthetic and Weight Preferences
Both 304 vs 316 stainless steel offer sleek, polished finishes, making them visually appealing for decorative applications. However, if your project demands reduced weight or thinner material with added strength, 316 stainless steel may provide a better balance between appearance and functionality.
Where to Choose the Best 304 vs 316 Stainless Steel for Your Project?
When it comes to choosing the right stainless steel for your project, you might be wondering, “Where can I source these materials?” Whether you’re working on a small-scale residential project or a large industrial operation, selecting the right supplier is critical for ensuring high-quality materials at competitive prices.
At DZS Metal, we specialize in providing both 304 vs 316 stainless steel that meets the stringent quality standards required for a wide range of industries. With years of experience in supplying stainless steel materials for sectors like construction, automotive, marine, food processing, and pharmaceuticals, we offer a reliable and cost-effective solution for all your stainless steel needs.

Our team is committed to delivering 304 and 316 stainless steel tailored to your specific project requirements, ensuring that you get the right material for the job. Whether you need high corrosion resistance for marine applications or affordable durability for general-purpose use, DZS Metal is your trusted partner in sourcing the best stainless steel materials.
Choose DZS Metal for all your stainless steel needs, and rest assured knowing you’re working with a company that understands the importance of quality, reliability, and timely delivery.
Conclusion: Making the Right Choice for Your Project
Selecting between 304 vs 316 stainless steel comes down to understanding your project’s specific needs. For general-purpose applications, 304 stainless steel offers affordability, versatility, and reliable corrosion resistance in standard environments. However, if your project involves exposure to saltwater, harsh chemicals, or extreme conditions, the superior durability and corrosion resistance of 316 stainless steel make it the better choice.
By carefully evaluating environmental factors, budget constraints, and longevity requirements, you can confidently choose the right material to ensure long-term performance and success.