Are you trying to decide between carbon steel vs stainless steel? Do you need a material that is strong, durable, or resistant to corrosion? Which one offers the best balance of cost, performance, and longevity? How do you know which steel type is the right fit for your project?
When evaluating carbon steel vs stainless steel, it’s clear that each material offers unique benefits tailored to different applications. Carbon steel is known for its high strength, cost-effectiveness, and versatility, making it ideal for construction, industrial machinery, and tool manufacturing. Stainless steel, in contrast, delivers exceptional corrosion resistance and a clean, polished appearance, making it the top choice for kitchenware, medical instruments, and marine environments. Ultimately, the decision between carbon steel vs stainless steel should be based on your project’s performance requirements, environmental conditions, and long-term goals.
Understanding the differences between carbon steel vs stainless steel is essential for making the right choice. In this article, we’ll explore their composition, durability, cost, and applications, helping you determine which metal is best suited for your specific needs. Let’s dive in!

Get Your Free Catalog Now!
What Is Carbon Steel?
In the discussion of carbon steel vs stainless steel, carbon steel stands out as one of the most widely used metals in the world, valued for its high strength, durability, and affordability. It is primarily composed of iron and carbon, with the carbon content playing a crucial role in determining its hardness, ductility, and overall strength. Unlike stainless steel, carbon steel lacks significant amounts of chromium, nickel, or molybdenum, which makes it more susceptible to corrosion—but also easier to machine and weld, especially in industrial and structural applications.
Composition of Carbon Steel
The primary difference between carbon steel vs stainless steel lies in its chemical composition. Carbon steel consists mainly of:
- Iron (Fe) – The base metal that provides structural integrity.
- Carbon (C) – The most important element, determining the steel’s hardness and strength.
- Manganese (Mn) – Enhances toughness and wear resistance.
- Silicon (Si) – Improves strength and hardness.
- Sulfur (S) and Phosphorus (P) – Often present in trace amounts; too much can make the steel brittle.
Unlike stainless steel, which contains at least 10.5% chromium, carbon steel lacks a protective chromium oxide layer, making it more prone to rust when exposed to moisture. However, its higher carbon content makes it stronger and harder, making it a preferred choice for construction, automotive, and heavy machinery applications.
Types of Carbon Steel
Carbon steel is classified based on carbon content, which influences its strength, ductility, and hardness. The four main types are:
1. Low Carbon Steel (Mild Steel) – 0.05% to 0.25% Carbon
Low carbon steel, also known as mild steel, contains the least amount of carbon, making it:
✔ Highly ductile and easily machinable.
✔ More affordable than higher-carbon steels.
✔ Easy to weld, making it ideal for construction and fabrication.
✖ Less hard and wear-resistant, requiring coatings for durability.
2. Medium Carbon Steel – 0.25% to 0.60% Carbon
Medium carbon steel strikes a balance between strength and ductility, offering:
✔ Higher strength and hardness than mild steel.
✔ Better wear resistance, making it suitable for mechanical parts.
✔ Moderate machinability and weldability.
✖ Less flexible, meaning it is more prone to cracking under stress.
3. High Carbon Steel – 0.60% to 1.5% Carbon
High carbon steel is very strong and wear-resistant, but it is also more brittle. It offers:
✔ Superior hardness, ideal for cutting tools and blades.
✔ Increased strength, making it resistant to deformation.
✖ Harder to machine and weld due to its rigidity.
✖ More susceptible to cracking if not handled properly.
4. Ultra-High Carbon Steel – Above 1.5% Carbon
Ultra-high carbon steel is the hardest and strongest of all carbon steels but is also the most brittle. It is primarily used in specialized applications where extreme strength is needed.
✔ Maximum hardness and durability.
✔ Best for wear-resistant tools.
✖ Extremely brittle and difficult to weld.
✖ Limited applications due to lack of flexibility.

How Carbon Steel Is Processed
The production of carbon steel involves several steps to enhance its properties:
- Iron Extraction:
- Extracted from iron ore using blast furnaces.
- Carbon Addition:
- Controlled carbon levels are introduced to achieve desired strength and hardness.
- Rolling & Shaping:
- The steel is rolled into sheets, bars, or structural shapes.
- Heat Treatment (if required):
- Processes like annealing, quenching, and tempering improve toughness and reduce brittleness.
- Coating & Finishing:
- Some carbon steel is galvanized, painted, or treated with anti-rust coatings.
What Is Stainless Steel?
When comparing carbon steel vs stainless steel, stainless steel is recognized as a versatile, corrosion-resistant alloy prized for its strength, durability, and sleek appearance. Unlike carbon steel, which is prone to rust, stainless steel contains at least 10.5% chromium, which reacts with oxygen to form a protective oxide layer that prevents corrosion. This unique property makes stainless steel an ideal choice for medical instruments, kitchenware, marine environments, and a wide range of industrial machinery applications.
Composition of Stainless Steel
Stainless steel is primarily composed of:
- Iron (Fe) – The base metal providing strength and structure.
- Chromium (Cr) (10.5% or more) – Forms a protective oxide layer, preventing rust and corrosion.
- Nickel (Ni) – Enhances strength, toughness, and corrosion resistance, especially in acidic environments.
- Molybdenum (Mo) – Increases resistance to pitting and crevice corrosion, making it suitable for marine and chemical applications.
- Carbon (C) (0.03% to 1.2%) – Strengthens the steel while maintaining ductility.
- Manganese (Mn), Silicon (Si), and Nitrogen (N) – Improve mechanical properties and oxidation resistance.
In the comparison of carbon steel vs stainless steel, one key difference is that stainless steel does not require additional coatings to prevent rust, as its chromium content naturally provides built-in corrosion resistance, unlike carbon steel.
Types of Stainless Steel
Stainless steel is classified into three main categories, each offering different mechanical and corrosion-resistant properties.
1. Austenitic Stainless Steel (Grades 304, 316)
Austenitic stainless steel is the most widely used type, known for its high corrosion resistance, excellent strength, and non-magnetic properties. It contains high levels of chromium (16-26%) and nickel (6-22%), making it highly resistant to oxidation and acidic environments.
✔ Excellent corrosion resistance in marine and food industries.
✔ Non-magnetic, making it ideal for medical and electrical applications.
✔ Easily weldable and formable.
✖ More expensive due to high nickel content.
2. Ferritic Stainless Steel (Grades 409, 430)
Ferritic stainless steel has moderate corrosion resistance and is magnetic. It contains lower nickel levels (or none at all), making it more affordable than austenitic stainless steel but less corrosion-resistant.
✔ More affordable due to lower nickel content.
✔ Good oxidation resistance at high temperatures.
✔ Magnetic properties useful for electrical applications.
✖ Less corrosion-resistant than austenitic grades.
✖ Not as strong or durable as high-nickel stainless steels.
3. Martensitic Stainless Steel (Grades 410, 420)
Martensitic stainless steel is strong, hard, and wear-resistant but has lower corrosion resistance than austenitic and ferritic grades. It contains 12-18% chromium and higher carbon content, making it ideal for cutting tools and high-strength applications.
✔ High strength and hardness, making it perfect for blades and tools.
✔ Can be heat-treated for increased durability.
✔ Moderate corrosion resistance but lower than austenitic grades.
✖ Brittle in high-hardness conditions.
✖ Less resistant to acids and moisture.

How Stainless Steel Is Processed
The manufacturing process of stainless steel involves several steps to enhance its strength, corrosion resistance, and finish:
- Melting & Alloying:
- Stainless steel starts as raw iron, mixed with chromium, nickel, and molybdenum.
- Refining & Casting:
- The molten metal is refined to remove impurities, then cast into slabs or billets.
- Hot Rolling & Cold Rolling:
- Hot rolling improves strength and shape, while cold rolling refines the surface finish.
- Heat Treatment & Hardening:
- Certain grades are annealed, quenched, or tempered to modify hardness.
- Surface Finishing:
- Stainless steel is polished, brushed, or coated depending on application requirements.
Strength & Durability: Carbon Steel vs Stainless Steel – Which One Is Stronger?
When comparing carbon steel vs stainless steel, strength and durability are two of the most important factors to consider. Both materials are used in construction, automotive, aerospace, and heavy machinery, but they perform differently under stress, impact, and environmental conditions.
Carbon Steel vs Stainless Steel: Which Has Higher Tensile Strength?
Tensile strength measures how much force a material can withstand before breaking. It is crucial in structural applications, bridges, automotive frames, and machinery where steel must endure heavy loads.
✔ Carbon Steel: Higher Tensile Strength in High-Carbon Grades
- Low-carbon steel (250–400 MPa) is soft and ductile, suitable for construction and fabrication.
- Medium-carbon steel (500–800 MPa) balances strength and flexibility, making it common in gears and axles.
- High-carbon steel (up to 1,200 MPa) is extremely strong, used in cutting tools, knives, and springs.
✖ However, high-carbon steel can be brittle—it is strong but may crack under high stress rather than bend.
✔ Stainless Steel: Tougher & More Impact-Resistant
- Austenitic stainless steel (485–700 MPa) is strong but flexible, making it ideal for medical tools and kitchenware.
- Martensitic stainless steel (up to 1,100 MPa) is hardened for cutting tools, turbines, and industrial equipment.
- Duplex stainless steel (600–900 MPa) is both strong and corrosion-resistant, used in marine and chemical industries.
✔ Stainless steel is not as strong as high-carbon steel, but it is more impact-resistant, meaning it absorbs shocks and sudden forces better.
Need Help? We’re Here for You!
Carbon Steel vs Stainless Steel: Which Offers Better Durability and Longevity?
✔ Carbon Steel: Strong but Requires Maintenance
- High durability in dry environments, commonly used in bridges, railway tracks, and tools.
- Prone to rust and corrosion, requiring coatings like galvanization or paint to extend its lifespan.
- Lasts for decades with proper maintenance, but needs regular inspection and protective treatment.
✔ Stainless Steel: Long-Lasting & Corrosion-Resistant
- Naturally corrosion-resistant due to chromium content, making it perfect for marine, food, and medical applications.
- Withstands humidity, chemicals, and extreme weather without deteriorating.
- Higher long-term durability with minimal maintenance, lasting 30+ years in outdoor or industrial settings.
✔ Stainless steel lasts longer than carbon steel in harsh environments, while carbon steel is more durable in dry conditions when protected against corrosion.
Corrosion Resistance: Carbon Steel vs Stainless Steel
When comparing carbon steel vs stainless steel, corrosion resistance is one of the most crucial factors. Carbon steel rusts faster than stainless steel due to differences in their composition.
Carbon Steel’s Corrosion Resistance
Carbon steel is made primarily of iron and carbon, without significant amounts of chromium. The absence of chromium means that carbon steel lacks a protective oxide layer, making it prone to rust when exposed to moisture, salt, or air. The iron in carbon steel reacts with oxygen and moisture, leading to iron oxide (rust) formation. This process is accelerated when carbon steel is uncoated.
- Prone to rust in moist or wet environments.
- Requires coatings (paint, galvanization, oil) to protect against corrosion.
- More vulnerable in environments with high humidity or salt exposure.
Stainless Steel’s Corrosion Resistance
Stainless steel contains at least 10.5% chromium, which reacts with oxygen in the air to form a protective chromium oxide layer. This oxide layer prevents the underlying iron from reacting with oxygen and moisture, stopping rust formation. Even if the surface is scratched, the chromium oxide layer self-heals, maintaining long-term protection against corrosion.
- Highly resistant to corrosion and rust in moist, humid, and salty environments.
- Ideal for marine, food processing, and medical industries.
- Higher chromium content in 316 stainless steel offers superior resistance to saltwater.
Machinability and Weldability of Carbon Steel vs Stainless Steel
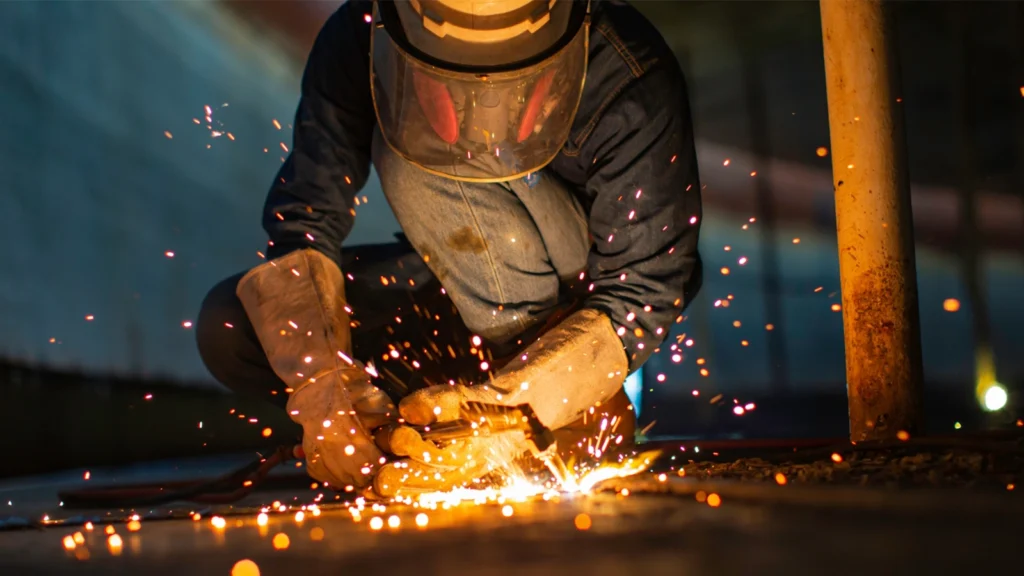
When comparing carbon steel vs stainless steel, machinability and weldability are critical factors that determine how easily each material can be cut, shaped, and joined. These properties not only affect production efficiency and costs, but also the quality and strength of the final product.
Carbon Steel vs Stainless Steel: Which Is Easier to Machine and Weld?
Carbon Steel’s Machinability and Weldability
Carbon steel is generally known for its excellent machinability and weldability, especially in low-carbon grades. Because carbon steel contains fewer alloying elements, it is relatively soft and easy to shape, making it a preferred choice for industrial applications that require high-volume production.
- Low-carbon steel is the easiest to machine and weld, requiring standard processes such as MIG, TIG, and stick welding without the need for special techniques or preheating.
- Medium-carbon steel provides a balance of strength and machinability, often used in gears, axles, and automotive parts. It may require preheating or controlled cooling during welding to reduce the risk of distortion.
- High-carbon steel is more difficult to machine due to its increased hardness, and while it is weldable, special processes like preheating or post-weld heat treatment are often required to avoid cracking and brittleness.
Advantages of Carbon Steel’s Machinability and Weldability:
✔ Easier to machine with conventional tools and processes.
✔ Widely used for welding due to good joint formation with minimal risk of defects.
✔ Low cost of machining and welding compared to stainless steel.
Challenges:
✖ High-carbon grades are more difficult to machine and may require special tooling.
✖ Brittle in high-carbon forms, requiring careful handling during welding.
Stainless Steel’s Machinability and Weldability
While stainless steel offers superior corrosion resistance and durability, it is more challenging to machine and weld compared to carbon steel. The high chromium content (usually 10.5% or more) and other alloying elements like nickel make stainless steel tougher, which increases the wear on cutting tools and requires more specialized processes.
- Austenitic stainless steel (e.g., 304, 316) is the most commonly used stainless steel and is relatively easier to machine than other grades due to its high ductility. However, it still requires careful tooling and precision to avoid excessive tool wear.
- Martensitic and ferritic stainless steels are much harder to machine and require specialized tooling and lower cutting speeds to prevent tool damage.
- Welding stainless steel is more challenging, especially for higher grades. While austenitic stainless steels are easier to weld and can be welded using standard processes, martensitic and ferritic steels may require precise heat control to avoid issues like distortion and cracking.
Advantages of Stainless Steel’s Machinability and Weldability:
✔ Superior corrosion resistance, making it ideal for harsh environments.
✔ Good weldability in austenitic grades, especially 304 and 316, which are commonly used in food processing, medical equipment, and marine applications.
✔ Strength and durability make it suitable for applications that require high performance over time.
Challenges:
✖ Harder to machine, especially in high-carbon or martensitic grades, requiring special tooling and careful techniques.
✖ More expensive to weld due to the need for precise control and specialized welding techniques to avoid defects.

Get Your Free Catalog Now!
Thermal Conductivity and Heat Resistance: Carbon Steel vs Stainless Steel – How Do They Perform at High Temperatures?
When comparing carbon steel vs stainless steel, thermal conductivity and heat resistance are critical factors in determining how each material performs in high-temperature environments. Both materials are used in applications where heat transfer and resistance to thermal degradation are important.
Thermal Conductivity: Carbon Steel vs Stainless Steel – Which Transfers Heat More Efficiently?
Carbon Steel’s Thermal Conductivity
Carbon steel has a relatively high thermal conductivity, meaning it is able to transfer heat more efficiently than stainless steel. This makes carbon steel a good choice for applications that require rapid heat conduction such as heat exchangers, cookware, and industrial machinery.
- Thermal conductivity of carbon steel is around 50 W/m·K, which is significantly higher than that of stainless steel.
- This makes carbon steel ideal for applications where heat distribution is critical, such as woks, griddles, and frying pans, where quick and even heating is required.
Stainless Steel’s Thermal Conductivity
In contrast, stainless steel has lower thermal conductivity than carbon steel, meaning it does not transfer heat as efficiently. However, this can be an advantage in some cases where heat retention or resistance to heat loss is important.
- Thermal conductivity of stainless steel is approximately 16 W/m·K, much lower than carbon steel.
- While stainless steel is not ideal for applications that require fast heat transfer, it is excellent for heat-resistant cookware, and insulated appliances.
Heat Resistance: Carbon Steel vs Stainless Steel – Which Steel Withstands High Temperatures Better?
Carbon Steel’s Heat Resistance
Carbon steel performs well in high-temperature environments but is more susceptible to damage when exposed to extremely high heat over extended periods. Typically, carbon steel can tolerate temperatures up to 500°C (932°F), but oxidation becomes an issue after prolonged exposure to heat.
- Low-carbon steel is generally resistant to heat deformation and retains its strength up to around 500°C. However, it oxidizes more quickly in high-heat applications.
- High-carbon steel is more brittle at elevated temperatures and can experience thermal degradation. It is best suited for high-strength applications but requires coatings or controlled environments to prevent rust.
Stainless Steel’s Heat Resistance
In the context of carbon steel vs stainless steel, stainless steel—particularly austenitic grades like 304 and 316—offers superior heat resistance. It can withstand extremely high temperatures, typically ranging from 800°C to 1,000°C (1,472°F to 1,832°F) depending on the specific grade. This exceptional thermal performance makes stainless steel the preferred material for applications in aerospace, chemical processing, and other high-temperature industrial environments.
- Stainless steel is not only resistant to oxidation but also retains its mechanical properties at high temperatures, making it the material of choice for high-performance applications.
- Grades such as 316 are specifically designed to handle extreme heat and are used in marine environments and high-temperature chemical plants.
Applications of Carbon Steel vs Stainless Steel
Applications of Carbon Steel
1. Construction and Infrastructure
Carbon steel is commonly used in the construction industry due to its high strength and affordability. It is ideal for structural components such as beams, columns, and reinforced concrete. Carbon steel is used for bridges, tunnels, and highways, where strength is a key factor, and corrosion resistance is not as critical.
2. Automotive and Transportation
In the automotive industry, carbon steel is often used for structural parts such as car frames, axles, gears, and suspension parts. Its strength and cost-effectiveness make it ideal for vehicle manufacturing. Carbon steel is also widely used in railway tracks and railroad cars.
3. Industrial Equipment and Tools
Carbon steel is commonly found in tools and machinery that require strength but do not need high corrosion resistance. It is ideal for cutting tools, industrial equipment, and heavy machinery parts such as shafts, gears, and blades.
4. Cookware and Kitchenware
Due to its excellent heat transfer properties, carbon steel is used in cookware like frying pans, woks, and griddles. It heats up quickly and distributes heat evenly, making it a popular choice in professional kitchens. However, carbon steel cookware needs regular seasoning to maintain its non-stick properties and prevent rust.
5. Agricultural and Mining Equipment
Carbon steel is ideal for heavy-duty agricultural and mining equipment. It is used in plows, tillers, harvesting machinery, and mining tools like drills and shovels. Its high strength makes it perfect for these tough, abrasive applications, although it may need protection from corrosion.
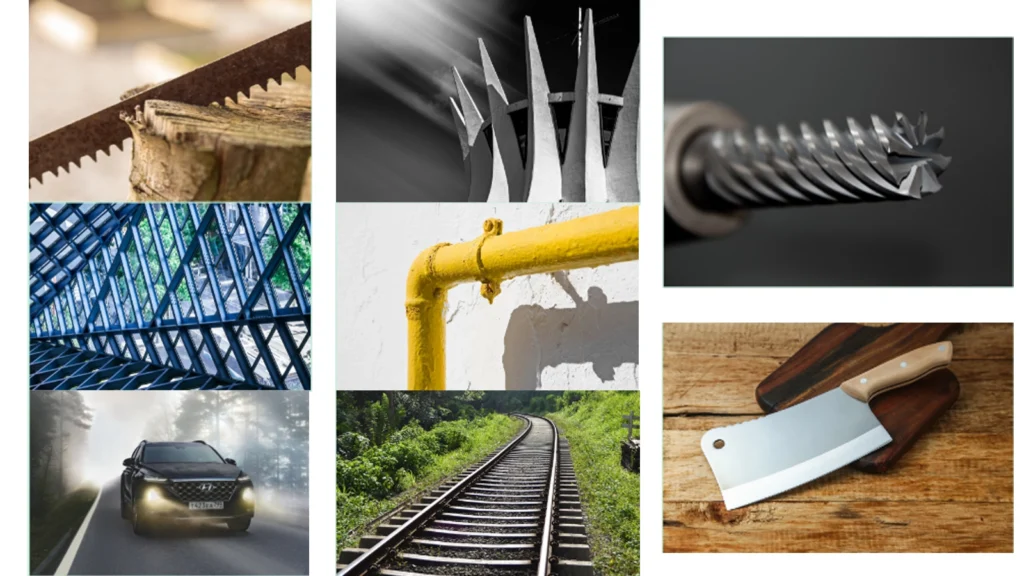
Applications of Stainless Steel
1. Medical and Pharmaceutical Equipment
Stainless steel is widely used in the medical and pharmaceutical industries because of its corrosion resistance, biocompatibility, and ease of sterilization. It is commonly found in surgical instruments, implants, medical devices, and hospital equipment like beds, trays, and scalpels.
2. Food and Beverage Industry
Due to its hygienic properties and resistance to corrosion, stainless steel is the material of choice for food processing equipment, kitchen appliances, and storage tanks. It is commonly used in brewing, dairy, and meat processing industries, where sanitary conditions are essential. Stainless steel kitchenware is also non-reactive with food, making it ideal for cookware, utensils, and countertops.
3. Chemical and Petrochemical Industry
In the chemical and petrochemical industries, stainless steel is used for reactors, pipelines, pressure vessels, and tanks due to its superior corrosion resistance to acids and chemicals. Stainless steel’s heat resistance makes it ideal for high-temperature processing applications.
4. Marine and Offshore Applications
Stainless steel is highly resistant to corrosion in saltwater environments, which makes it ideal for marine and offshore applications. It is used in boat hulls, ship components, offshore oil rigs, and marine fasteners. Stainless steel’s resistance to pitting and crevice corrosion ensures long-term durability in harsh marine environments.
5. Architecture and Construction
In the field of architecture, stainless steel is valued for its modern aesthetic, durability, and resistance to corrosion. It is commonly used for facades, cladding, roofing, elevators, and handrails. Stainless steel is also widely used in decorative applications like sculptures and art installations due to its polished finish and long-lasting appearance.

Maintenance: Carbon Steel vs Stainless Steel
When comparing carbon steel vs stainless steel, maintenance is a critical factor that affects long-term performance and cost. While both materials have their strengths, they require different levels of care and attention to maintain their integrity and appearance over time.
Maintenance of Carbon Steel
Carbon steel is more vulnerable to rust and corrosion compared to stainless steel due to the lack of a protective oxide layer. To keep carbon steel in optimal condition, regular maintenance is essential.
- Rust Prevention: Carbon steel needs to be coated with paint, oil, or galvanization to prevent oxidation. If left untreated, it will begin to rust when exposed to moisture or humidity.
- Cleaning: It is important to clean carbon steel regularly to remove any moisture or contaminants that may lead to rust. After exposure to water, it should be dried immediately to avoid corrosion.
- Protective Coatings: Applying protective coatings like wax or oil can help prevent rust, especially for carbon steel cookware. Reapplication of coatings may be needed periodically to ensure protection.
- Storage: Carbon steel should be stored in dry places to avoid moisture contact. When not in use, keeping carbon steel tools or equipment in a dry environment is crucial to prevent corrosion.
Need Help? We’re Here for You!
Maintenance Challenges with Carbon Steel:
✔ Requires regular protective coatings (paint, oil, galvanization).
✔ Needs frequent cleaning to prevent rusting.
✔ More vulnerable to rust without consistent care.
Maintenance of Stainless Steel
Stainless steel, due to its corrosion resistance, requires minimal maintenance compared to carbon steel. The chromium oxide layer that forms naturally on stainless steel protects it from rust and corrosion, making it easier to care for.
- Cleaning: Stainless steel should be cleaned regularly to maintain its appearance and remove dirt, salt, or grease that may accumulate. A simple wipe down with mild detergent and water is often sufficient.
- Preventing Staining: While stainless steel is resistant to corrosion, it can still develop fingerprints or water spots. To maintain its shine, periodic polishing or buffing may be needed, especially in high-visibility areas like kitchen appliances.
- Scratches and Stains: Scratches can occur, but stainless steel’s self-healing properties allow the material to repair itself to some degree. In environments with heavy exposure to saltwater or chemicals, you may need to apply a protective coating or polish to ensure long-term durability.
- Storage: Stainless steel requires little special care for storage. However, storing it in a clean, dry environment will help maintain its aesthetic and corrosion resistance over time.
Maintenance Advantages with Stainless Steel:
✔ Minimal maintenance due to corrosion resistance.
✔ Easy to clean and maintain with mild detergents.
✔ Self-healing properties that help resist corrosion and stains.

Cost Comparison: Carbon Steel vs Stainless Steel
One of the key factors in deciding between carbon steel vs stainless steel is cost. Both materials have their own pricing structures, which vary depending on factors like grade, alloying elements, and processing methods.
Cost of Carbon Steel
When comparing carbon steel vs stainless steel, cost is one of the most noticeable differences. Carbon steel is typically more affordable because it contains fewer alloying elements, making it less expensive to produce. Its simple composition—primarily iron and carbon—results in lower manufacturing costs, especially for low-carbon steel, which is widely used in cost-sensitive applications.
- Low-carbon steel is the least expensive, making it ideal for construction, automotive, and machinery applications.
- Medium-carbon steel and high-carbon steel are more expensive than low-carbon steel due to their increased strength and hardness, but they are still more affordable compared to stainless steel.
Factors that contribute to the cost of carbon steel:
- Grade of carbon steel: Higher grades with more carbon content are more expensive.
- Processing: Extra processes like coating (e.g., galvanization) or heat treatment can add to the cost.
- Bulk purchases: Carbon steel tends to be cheaper in large quantities, making it more cost-effective for mass production.
Cost Benefits of Carbon Steel:
✔ Lower upfront costs due to simpler composition.
✔ Affordable for large-scale applications and mass production.
✔ Cheaper processing costs compared to stainless steel.
Cost of Stainless Steel
In the carbon steel vs stainless steel comparison, stainless steel is significantly more expensive due to its complex composition, which includes high levels of chromium, nickel, and occasionally molybdenum. These alloying elements enhance its corrosion resistance, heat resistance, and overall durability, but they also contribute to a higher production cost compared to carbon steel.
- 304 stainless steel, which is one of the most common grades, is moderately priced compared to higher grades but still more expensive than carbon steel.
- 316 stainless steel, which contains molybdenum for enhanced corrosion resistance, is among the most expensive stainless steel grades.
Factors that contribute to the cost of stainless steel:
- Alloying elements: The more chromium, nickel, or other elements in the alloy, the higher the cost.
- Processing: Stainless steel requires specialized tools for machining and welding, making it more expensive to work with.
- Surface finishes: Polished or brushed finishes add to the overall cost of stainless steel products.
Cost Considerations for Stainless Steel:
✔ Higher initial cost due to alloying elements.
✔ More expensive to machine and fabricate due to its hardness.
✔ Long-term savings due to low maintenance and durability in corrosive environments.
Carbon Steel vs Stainless Steel: Cost Comparison in Real-World Applications
Factor | Carbon Steel | Stainless Steel |
---|---|---|
Upfront Material Cost | ✔ Lower cost due to simpler composition | ✖ Higher cost due to alloying elements (chromium, nickel, etc.) |
Processing Costs | ✔ Lower processing costs | ✖ Higher processing costs due to machining and welding difficulties |
Maintenance Costs | ✖ Requires coatings and maintenance to prevent rust | ✔ Lower maintenance costs (resistant to rust, minimal care) |
Durability & Longevity | ✖ Lower lifespan in corrosive environments | ✔ Higher lifespan due to corrosion resistance and durability |
Long-Term Cost Efficiency | ✖ Higher cost of replacement and maintenance in harsh environments | ✔ Higher initial cost but more cost-effective in the long run |
Which Is More Cost-Effective: Carbon Steel vs Stainless Steel?
- Carbon steel is the more affordable option upfront. It is ideal for applications where corrosion resistance is not a critical factor, and where the material does not require exposure to harsh environments. Carbon steel is best for shorter-term projects, construction, and general machinery where cost savings are a priority.
- Stainless steel, while more expensive, offers superior corrosion resistance, heat resistance, and durability, making it a better choice for long-term projects or those exposed to extreme conditions. The higher initial cost of stainless steel is often offset by reduced maintenance, longer lifespan, and lower replacement costs over time.
Need Help? We’re Here for You!
Environmental Impact and Sustainability: Carbon Steel vs Stainless Steel
As industries move toward more sustainable practices, the environmental impact of materials has become a crucial consideration. When comparing carbon steel vs stainless steel, it’s important to look beyond just performance and cost—sustainability, carbon footprint, and recyclability all play a role in responsible material selection.
Environmental Impact of Carbon Steel
1. Raw Material Extraction
Carbon steel is made primarily from iron ore and coal, both of which have significant environmental impacts. Mining these resources involves land disruption, high energy use, and greenhouse gas emissions, especially when blast furnaces are used in the smelting process.
2. Energy Consumption
In the carbon steel vs stainless steel discussion, carbon steel production generally requires less energy, especially in low-carbon grades. However, the reliance on coal-based manufacturing methods leads to higher carbon dioxide (CO₂) emissions, making carbon steel a more significant contributor to the global carbon footprint compared to stainless steel.
3. Corrosion and Longevity
Since carbon steel is prone to rust, it often needs to be replaced or maintained more frequently, which can result in higher cumulative environmental impact over time. Coatings like paints or galvanization may also contain chemicals that are not environmentally friendly.
4. Recyclability
Carbon steel is fully recyclable, and it is one of the most recycled materials globally. The steel industry uses a high percentage of scrap steel, reducing the demand for virgin materials and lowering emissions during remanufacturing.
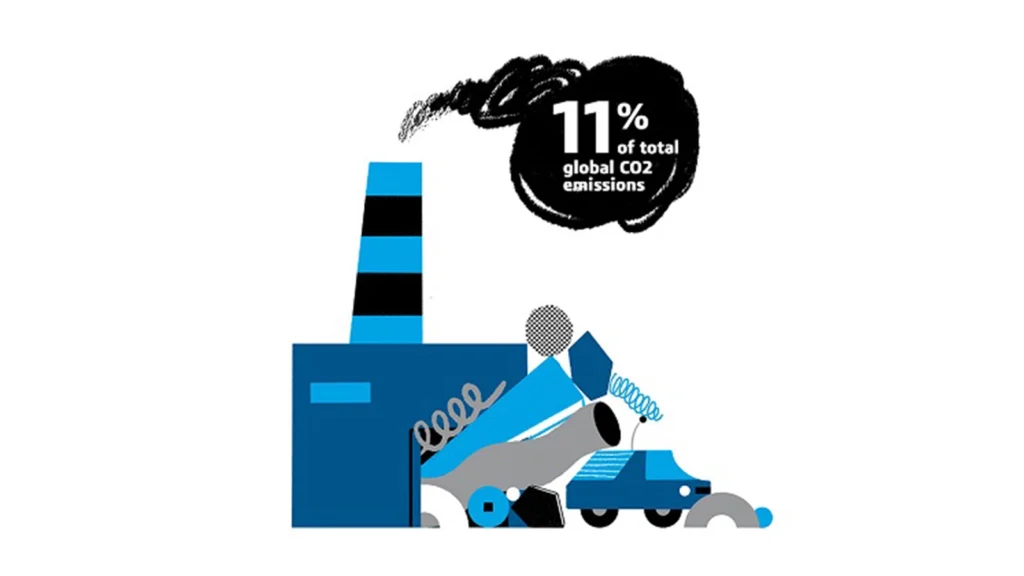
Environmental Impact of Stainless Steel
1. Raw Material Extraction
Stainless steel requires the extraction of more alloying elements like chromium, nickel, and molybdenum, which can be more resource-intensive and environmentally damaging if not managed responsibly.
2. Energy Use in Production
When evaluating carbon steel vs stainless steel, it’s important to note that producing stainless steel consumes more energy per ton due to the complexity of its refining and alloying processes. However, this higher energy use is partially offset by stainless steel’s superior durability, which reduces the need for frequent replacements and contributes to its long-term sustainability.
3. Durability and Lifecycle
Stainless steel lasts significantly longer in harsh environments, reducing the need for maintenance, coatings, and replacements. This contributes to a lower environmental impact over its lifecycle, especially in marine, medical, or industrial environments.
4. Recyclability and End-of-Life Impact
Stainless steel is also 100% recyclable, and the recycling process maintains the material’s integrity, allowing for infinite reuse. Most stainless steel products contain a high percentage of recycled content, often exceeding 60%–80%, which greatly reduces environmental footprint.
Need Help? We’re Here for You!
Choosing the Right Steel for Your Project: Carbon Steel vs Stainless Steel
After reviewing the key differences in composition, strength, corrosion resistance, machinability, cost, and sustainability, it’s clear that the decision between carbon steel vs stainless steel should be based on your project’s specific requirements.
If your priority is maximum strength, affordability, and ease of fabrication, carbon steel is likely the better choice—especially in industries like construction, automotive, and industrial equipment. However, if your application demands high corrosion resistance, aesthetic appeal, or long-term durability with minimal maintenance, stainless steel is undoubtedly the superior option.
💡 Need Expert Guidance on Steel Selection?
That’s where we come in.

At DZS Metal, we specialize in supplying high-quality carbon steel and stainless steel parts to industries across North America, Europe, Japan, and South Korea. With five advanced production lines and years of experience in casting, machining, forging, and sheet metal, we are proud to be a one-stop B2B solution for global buyers who need precision, quality, and reliability—without breaking the budget.
We understand the real-world challenges procurement professionals face—balancing cost, lead times, and quality control. Our team is here to guide you through material selection, help with technical drawing reviews, and ensure on-time delivery, backed by certifications and full quality inspection services.
Whether you’re sourcing custom carbon steel parts for industrial machinery, or stainless steel components for medical or food-grade applications, we tailor every solution to fit your exact needs.
🔧 Let’s Build Something Stronger Together
Choosing between carbon steel vs stainless steel isn’t just about metal—it’s about making the right decision for your project’s performance, timeline, and bottom line.
Let DZS Metal be your trusted manufacturing partner.