Have you ever wondered what makes iron melt at a specific temperature? Why does iron transition from solid to liquid, and how does this affect industries like casting and forging? The iron melting point is not just a scientific concept—it’s crucial to many metalworking processes. Whether you’re producing automotive parts, constructing machinery, or shaping materials, the melting point of iron ensures quality and efficiency. In this article, we’ll explore the science and applications that make this property so important.
Understanding the science behind the iron melting point takes us into the heart of metallurgy, where we examine how temperature and molecular structure dictate the behavior of iron. At a specific temperature, iron transforms from solid to liquid, enabling processes like iron casting and forging. But what factors affect this transformation? How does the addition of other elements, like carbon or manganese, influence the melting point of iron and its alloys? We’ll explore the atomic structure, the role of pressure, impurities, and how these elements shape the melting process, revealing insights that can improve material quality and manufacturing results.
Join us as we explore the secrets of iron’s melting point. From ancient forges to modern industries, the melting point of iron has shaped progress for centuries. Understanding phase transformations helps us grasp the forces within iron, making it vital for metal fabrication. Whether you’re an industry professional or curious about iron’s behavior under heat, this guide will deepen your understanding of one of Earth’s most critical materials.

What is the Melting Point of Iron?
The iron melting point refers to the specific temperature at which iron changes from a solid to a liquid. For pure iron, this occurs at approximately 1,538°C (2,800°F). This temperature is a crucial factor in several industrial processes, including iron casting, forging, and machining, where understanding the melting point of iron ensures proper handling and high-quality results.
To put it into perspective, the iron melting point in Celsius is 1,538°C, which is 2,800°F in Fahrenheit. In Kelvin, an important temperature scale in scientific contexts, the melting point of iron is 1,811K. These values are essential for controlling temperatures in furnaces, helping engineers and metalworkers optimize processes like casting and forging. Understanding the melting point of iron in these various units also provides insight into how iron behaves under extreme heat, impacting everything from industrial applications to experimental metalworking.
Need Help? We’re Here for You!
Factors Affecting Iron’s Melting Point
The melting point of iron is influenced by several factors, from alloying elements to external conditions like pressure and impurities. These factors can significantly alter the temperature at which iron transitions from solid to liquid, and understanding them is crucial for optimizing metalworking processes.
One of the key influences on the iron melting point is the presence of alloying elements. Adding elements such as carbon and manganese can lower the melting point of iron. For instance, cast iron, which contains a higher amount of carbon, has a melting point that ranges between 1,200°C – 1,300°C (2,190°F – 2,370°F), lower than the melting point of pure iron. On the other hand, pure iron has a melting point of 1,538°C (2,800°F). The alloying process creates different forms of iron, each with distinct characteristics and melting points.
Pressure also plays a role in the melting point of iron. In high-pressure environments, the iron melting point may increase. This phenomenon is particularly relevant in specialized industrial applications where high pressures are involved, such as in deep-sea operations or high-pressure casting.
Another critical factor that affects the melting point of iron is the presence of impurities. Elements like sulfur, phosphorus, and oxygen can lower the melting point of iron, leading to the formation of slag or other by-products. These impurities can also affect the material’s integrity, making it more susceptible to defects during casting and forging.
In addition, temperature influences such as the melting point of iron oxide and the melting point of iron chloride also come into play. Iron oxide, which forms when iron is exposed to oxygen, has a much higher melting point than pure iron, making it a crucial consideration when working with iron in oxidizing environments.
Lastly, it’s important to compare the melting point of iron to steel, as they differ significantly due to the presence of carbon and other alloying elements in steel. While the melting point of steel can vary depending on the specific alloy, it generally ranges from 1,370°C to 1,510°C (2,500°F to 2,750°F), which is lower than pure iron but higher than cast iron.
Understanding the Science Behind Iron’s Melting Point
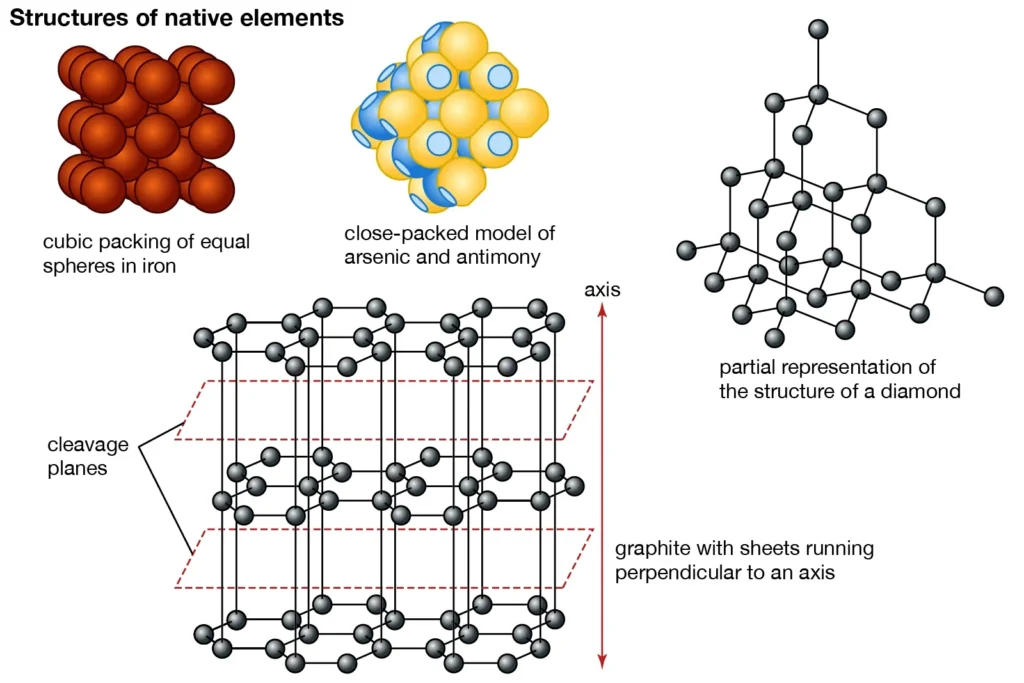
To fully grasp the iron melting point, it’s essential to explore the atomic structure and the molecular behavior of iron. In its solid state, iron has a body-centered cuic (BCC) crystalline structure, where the atoms are arranged in a specific pattern that influences how the material responds to heat. When iron is heated, its atoms begin to vibrate more rapidly, and at the melting point of iron, these vibrations become strong enough to break the bonds between the atoms. This transition from solid to liquid is a direct result of the iron’s melting point, which is the temperature at which the molecular bonds are overcome by heat, causing the material to liquefy.
The physics and chemistry behind this transformation are key to understanding why iron’s melting point is relatively high. The heat applied to the iron adds kinetic energy to the atoms, which causes them to move faster and overcome the forces holding them in place. The energy required to break these bonds is significant, which is why iron’s melting point sits at around 1,538°C (2,800°F). This is much higher than metals like aluminum, which have weaker atomic bonds. The strength of the metallic bonds in iron is a crucial factor in this high melting point of iron, as these bonds need a considerable amount of energy to be disrupted.
Why is iron’s melting point so high compared to other metals? The melting point of iron is a reflection of the strong atomic bonds formed by iron atoms in the BCC structure. The tightly packed atoms in iron’s crystalline structure create robust bonds, requiring more heat energy to break. Additionally, iron’s melting point is also influenced by the density of the metal and its atomic number, which contributes to the strong forces between the atoms. This is why iron’s melting point is higher than metals like aluminum or copper, which have weaker atomic structures.
In summary, the high melting point of iron is a result of its strong atomic bonds, dense crystalline structure, and the energy required to overcome these bonds. This understanding of the iron melting point is vital for industries such as metallurgy, casting, and forging, where precise control of temperature is needed to work with molten iron effectively.
Need Help? We’re Here for You!
Historical Significance of Iron’s Melting Point
The discovery of iron’s melting point was a landmark moment in the history of metallurgy, forever changing the way humans interacted with iron and its alloys. Before understanding the melting point of iron, early blacksmiths and metalworkers could heat iron to a point where it could be shaped through forging—but they lacked the ability to melt it completely.
Once the melting point of iron was discovered, it revolutionized metalworking by enabling iron casting, the process of pouring molten iron into molds to create more complex shapes. The melting point of iron opened the door to the mass production of iron-based objects, from tools and weapons to structural components, influencing the course of civilization.
The ability to melt iron introduced new possibilities. Iron casting, made possible by reaching and maintaining the iron melting point, allowed for the creation of durable, precise metal products. For example, cast iron, which has a melting point of iron lower than pure iron, became a key material in the construction of early bridges, tools, and machinery.
The knowledge of iron’s melting point was essential for forging a stronger economy. Industries could now mass-produce high-quality iron products, advancing both manufacturing and construction.
With the advent of the Industrial Revolution, understanding iron’s melting point played a crucial role in scaling up metal production. As iron melting point knowledge advanced, larger and more efficient furnaces were developed, enabling iron to be melted and cast at an industrial scale.
This knowledge also led to the creation of steel, a much stronger alloy that became essential in the construction of railways, buildings, and machines. The ability to manipulate the melting point of iron was central to the development of the steel industry, shaping the backbone of modern industrialization.

Even today, the melting point of iron remains an essential factor in metallurgical processes. From iron casting to steel production, industries rely on a deep understanding of iron’s melting point to optimize the manufacturing of everything from automobiles to infrastructure components. The melting point of iron continues to be crucial for controlling temperature and quality in modern production lines, making it one of the most significant properties in metallurgy.
Melting Points of Different Types of Iron
Type of Iron | Iron Melting Point | Key Characteristics and Applications |
---|---|---|
Pure Iron | 1,538°C (2,800°F) | Pure iron’s melting point is the highest among iron types, making it ideal for high-temperature applications like forging and machining. Its iron melting point ensures its stability under extreme heat. |
Cast Iron | 1,200°C – 1,300°C (2,190°F – 2,370°F) | The iron melting point of cast iron is lower than pure iron due to carbon content, making it easier to melt and cast. Commonly used in machinery, engine blocks, and pipes. |
Ductile Iron | 1,200°C – 1,300°C (2,190°F – 2,370°F) | Ductile iron has a melting point of iron similar to cast iron, offering greater strength and ductility. Ideal for applications in piping, valves, and gears. |
Galvanized Iron | Approximately 1,538°C (2,800°F) (without zinc coating) | Galvanized iron has a melting point of iron similar to pure iron, but the zinc coating impacts behavior at high temperatures, making it ideal for construction and automotive applications. |
Gray Cast Iron | 1,200°C – 1,300°C (2,190°F – 2,370°F) | The melting point of iron in gray cast iron is lower, making it ideal for machinery and automotive components that require high strength and wear resistance. |
Wrought Iron | 1,538°C (2,800°F) | Wrought iron’s melting point is the same as pure iron, making it ideal for forging and structural applications where malleability and strength are necessary. |
Cast Iron vs Steel | Cast Iron: 1,200°C – 1,300°C Steel: 1,370°C – 1,510°C (2,500°F – 2,750°F) | Steel’s melting point is higher than cast iron’s melting point due to alloying elements like carbon and manganese, making it more suitable for high-strength applications. |
The Boiling Point of Iron and Its Comparison to Melting Point
The iron melting point and the boiling point of iron are two critical temperatures that define the behavior of iron under heat, each with its own significance. The iron melting point refers to the temperature at which iron transitions from solid to liquid, and for pure iron, this occurs at 1,538°C (2,800°F). In contrast, the boiling point of iron is the temperature at which iron transforms from a liquid to a gas, and this occurs at 2,862°C (5,184°F).
While the melting point of iron is essential for processes like casting and forging, the boiling point of iron plays a less direct role in metalworking but is crucial for controlling the behavior of molten iron in high-heat environments.
One of the key differences between the iron melting point and the boiling point of iron is the amount of energy required to break the atomic bonds. When iron reaches its melting point, enough heat is provided to weaken the bonds between atoms, allowing iron to flow as a liquid. However, when iron reaches its boiling point, even more energy is needed to overcome the remaining bonds between the liquid atoms, leading to vaporization.
This higher energy requirement explains why the boiling point of iron is significantly higher than the iron melting point.
Understanding both the melting point of iron and the boiling point of iron is crucial in metal fabrication and industrial applications. The iron melting point is used to determine the ideal temperature for casting iron, allowing molten iron to be poured into molds without reaching temperatures where it would begin to vaporize.
On the other hand, the boiling point of iron must be understood to ensure that molten iron does not reach dangerously high temperatures during processes like steel production, where precise temperature control is necessary. Reaching the boiling point of iron can cause excessive vaporization, material loss, and unsafe working conditions.
How to Melt Iron: Step-by-Step Guide
Melting iron is a critical process in many industries, including casting, forging, and machining. Understanding the melting point of iron is essential to achieving the desired results, ensuring quality, and maintaining safety throughout the process. Below is a step-by-step guide on how to melt iron efficiently:
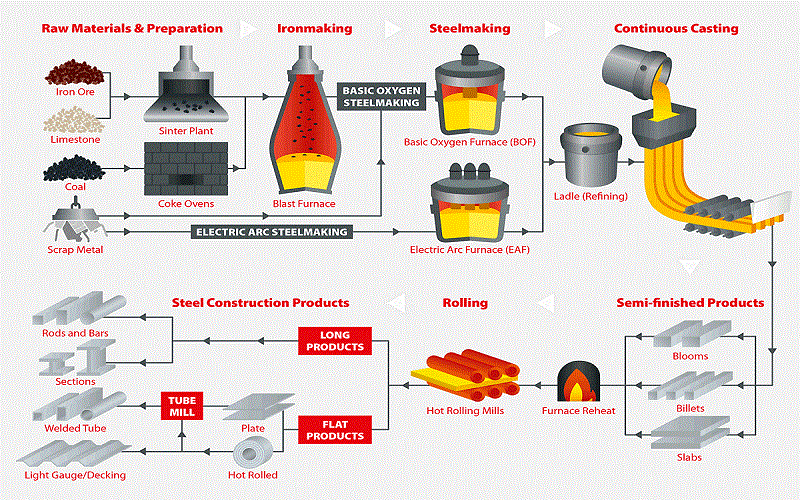
Step 1: Obtain Iron Ore or Scrap Iron
The first step in melting iron is to obtain the raw materials. This can be iron ore mined from the earth or scrap iron gathered from previous metalworking processes. The type of raw material you choose will depend on the iron melting point and the final product requirements.
Step 2: Remove Impurities
Before the iron is melted, it’s important to remove any impurities such as dirt, rust, or oils that may be present. This step ensures that the iron does not contain contaminants that could affect the melting point or the final quality of the molten iron.
Step 3: Choose the Right Iron Furnace Type
Different types of furnaces are used for melting iron, such as blast furnaces for large-scale operations or induction furnaces for smaller quantities. The furnace type should be selected based on the iron melting point and the production volume.

Get Your Free Catalog Now!
Step 4: Load Iron into the Furnace
Once the impurities are removed, the raw iron is loaded into the furnace. The furnace is carefully preheated to ensure it reaches the iron melting point without wasting energy or risking structural damage to the material.
Step 5: Heat Raw Materials to the Melting Point of Iron
The iron is heated until it reaches its melting point, which for pure iron is 1,538°C (2,800°F). During this stage, precise control of the furnace’s temperature is essential to ensure that the iron melts uniformly without reaching excessively high temperatures that could cause overheating or vaporization.
Step 6: Monitoring the Furnace’s Temperature and Conditions
Throughout the melting process, the temperature inside the furnace must be carefully monitored. Temperature sensors or thermocouples are often used to ensure that the furnace temperature stays within the optimal range, just below the boiling point of iron, to prevent the iron from vaporizing.
Step 7: Remove Contaminants like Slag and Other Impurities
As the iron melts, impurities such as slag will float to the surface. These contaminants must be removed to maintain the purity of the molten iron and prevent any defects in the final product. Removing slag ensures the iron melting point isn’t affected by unwanted elements.
Step 8: Pour Molten Iron into Molds for Casting
Once the iron has reached its melting point, it’s ready to be poured into molds. The molten iron should flow smoothly into the molds to create the desired shapes, whether for industrial machinery, automotive parts, or other applications. The melting point of iron dictates the necessary temperature for this process, ensuring that the molten metal maintains its fluidity and quality.
Step 9: Cooling the Molten Iron
After the iron is poured into molds, it begins to cool and solidify. The rate of cooling is crucial in determining the final structure of the iron. The cooling rate can impact the grain structure and strength of the iron, making it an important part of the casting process.
Step 10: Check the Quality of the Final Iron Product
Once the iron has cooled, it is removed from the mold and inspected for quality. Common inspection techniques include visual checks, ultrasonic testing, or X-ray examination. Ensuring that the iron has solidified correctly is important for achieving the desired mechanical properties and meeting quality standards.
Throughout this entire process, understanding the melting point of iron is vital. The iron melting point governs many aspects of the process, from furnace temperature control to mold filling. Without precise control over the melting point of iron, the result can be poor-quality products, wastage of material, and inefficient energy usage. Whether you are using pure iron or cast iron, knowing the melting point ensures that you can achieve the correct consistency and quality in the molten iron, leading to better casting results and stronger, more reliable iron products.

Get Your Free Catalog Now!
Practical Applications of Iron’s Melting Point Knowledge
Understanding the melting point of iron is not just important for academic purposes—it is essential in a variety of industries that rely on metalworking processes such as casting, forging, machining, and welding. Knowing the iron melting point allows manufacturers to optimize processes, improve quality, and ensure that iron products meet the required standards for strength and durability. Below, we discuss the influence of the melting point of iron across several key industries, as well as practical tips for achieving high-quality results.
Impact of the Iron Melting Point on Metalworking
The melting point of iron directly impacts the metalworking processes used to manipulate and shape iron. Whether you’re using pure iron or cast iron, understanding the iron melting point is crucial to control the flow of molten metal during casting, the precision during forging, and the quality during machining.
- Casting: The iron melting point determines the temperature required to make iron flow smoothly into molds, creating products like engine blocks, pipes, and machine components. By heating iron to its melting point, it becomes more fluid, allowing it to fill complex molds more effectively and form intricate shapes.
- Forging: In forging, iron is heated to a temperature just below its melting point to make it malleable, but not to the point where it turns into liquid. By controlling the melting point of iron, manufacturers can ensure that the metal remains solid enough to be shaped while retaining its strength and integrity.
- Machining: In machining processes, where iron is cut or shaped with tools, the melting point of iron is a key factor in preventing thermal distortion. Excessive heat can cause warping, deformation, or loss of precision, while too little heat can result in inefficient cutting or incomplete shaping.
- Welding: For welding, the iron melting point dictates the temperature at which molten iron can be joined together. If the iron reaches temperatures beyond its melting point, it can cause oxidation or poor bonding. Careful control of temperature ensures strong, durable joints without damaging the material.
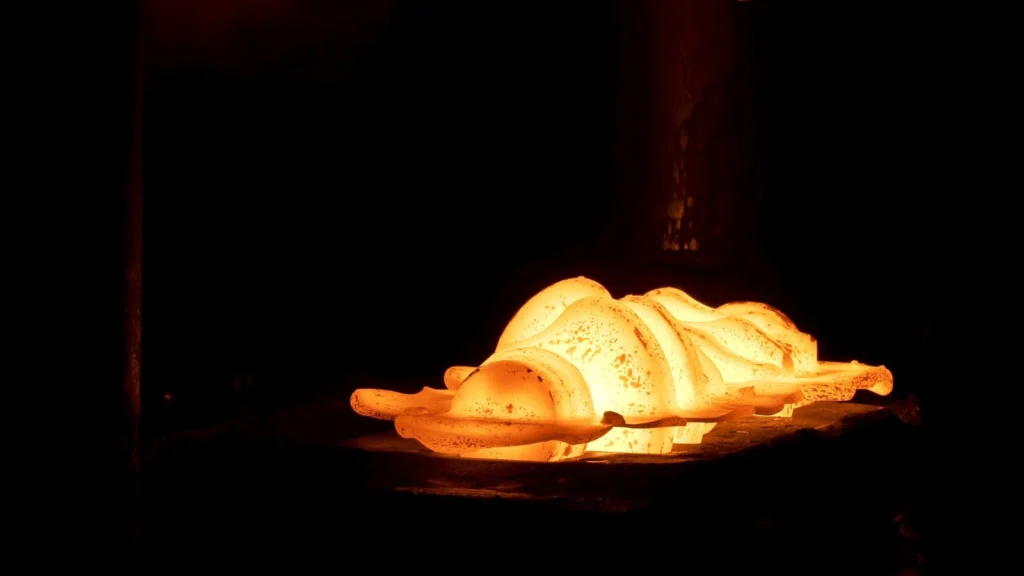
Significance in Key Industries
The melting point of iron is essential in various industries that depend on iron products for their functionality and durability. By knowing the melting point of iron, professionals can ensure the proper handling of molten iron, leading to high-quality results across several sectors.
- Automotive Industry: The melting point of iron is critical when manufacturing components like engine blocks, pistons, and brake parts. Cast iron and ductile iron are used extensively due to their ability to withstand high temperatures, and understanding their melting points is key to producing parts with the right strength and durability.
- Construction: In the construction industry, iron’s melting point ensures that critical structural components like beams, columns, and pipes are made to the proper specifications. By understanding how to control the temperature and iron melting point, construction materials can resist deformation under pressure and extreme conditions.
- Agriculture: In the agriculture industry, machinery parts like plows and tractor components are often made from iron. Understanding the melting point of iron allows manufacturers to create durable components that can withstand the stresses of farm environments.
- Valve Manufacturing: The melting point of iron is also significant in valve manufacturing, where precision is crucial. Components made from ductile iron or cast iron must be accurately molded and treated to withstand pressure and temperature changes in fluid systems. Knowing the melting point of iron ensures proper casting and integrity of the final product.
Practical Tips for Using the Iron Melting Point to Achieve High-Quality Results
To achieve optimal results in metalworking and iron casting, here are practical tips for utilizing the melting point of iron:
- Precise Temperature Control: Always ensure that the furnace or melting equipment maintains a temperature just below or at the iron melting point. Overheating can lead to oxidation, material loss, or inconsistent results.
- Use Quality Materials: Select the right type of iron based on its melting point. For instance, cast iron has a lower melting point than pure iron, making it more suitable for casting but less ideal for processes like forging where higher strength is needed.
- Monitor Impurities: Impurities can lower or affect the melting point of iron, so it’s crucial to remove contaminants like slag before and during the melting process. This ensures that the final product maintains its structural integrity.
- Ensure Proper Cooling: After the iron is melted and cast, controlling the cooling process is essential. The melting point of iron directly impacts the solidification rate, affecting the grain structure and mechanical properties of the finished product.
- Understand Alloying Effects: Different alloys have different melting points of iron. For example, high-carbon steel has a lower melting point compared to pure iron, so temperature management is key to achieving the desired physical properties in the final alloy.
Need Help? We’re Here for You!
Innovations and Future Prospects in Iron’s Melting Point Research
Research into the iron melting point continues to evolve, offering exciting prospects for the future of metallurgy. As industries strive to become more efficient, understanding and controlling the melting point of iron has become a key focus. Recent advancements aim to optimize iron melting point control for more energy-efficient industrial processes, ultimately reducing production costs and improving overall performance.
One of the most notable areas of innovation is the development of new alloys designed to either lower or raise the melting point of iron. By incorporating elements like nickel, chromium, and manganese, metallurgists can create iron alloys with tailored melting points to suit specific applications. Lowering the melting point of iron can improve casting and forging processes, making them more efficient and cost-effective. Conversely, raising the melting point of iron could produce materials that perform better under extreme heat conditions, which is particularly beneficial for industries like aerospace, energy, and automotive manufacturing.
Researchers are also exploring ways to control the melting point of iron with greater precision. Advances in furnace technology and temperature regulation allow for more accurate control of the iron melting point, leading to better casting outcomes, higher-quality products, and fewer defects in the final materials. By optimizing the iron melting point in industrial settings, manufacturers can ensure that the metal melts at the most efficient temperature, reducing energy consumption and ensuring a cleaner, safer environment.
The future of iron melting point research is focused on enhancing metalworking techniques through better temperature management. This includes developing more efficient ways to heat iron to its melting point using less energy while maintaining optimal results. Such innovations have the potential to revolutionize steel production, metal fabrication, and other sectors that rely heavily on iron melting point control.
Conclusion
Mastering the iron melting point is key to optimizing manufacturing and metalworking techniques. It plays a vital role in processes like casting, forging, and machining, ensuring high-quality results and efficient production. Understanding the iron melting point is essential for improving metal fabrication processes and enhancing product strength and durability. As iron melting point research advances, we can expect even more precise control and innovation, leading to better materials and more efficient industrial applications.

At DZS Metal, we specialize in providing high-quality casting, machining, forging, and sheet metal parts for a variety of industries, including automotive, construction, and petrochemical. With a focus on cost-effective solutions and exceptional product quality, we pride ourselves on understanding the precise melting points of iron and other metals to optimize our production processes. Whether you’re looking for iron castings or customized metal components, our team is here to help. Visit our website at www.dzsmetal.com to learn more about how we can meet your manufacturing needs and provide reliable, high-performance metal solutions.